Sometimes it’s not the flashy things that make you really appreciate 3D printing. Sure, the beautiful and intricate jewelry, the precisely replicated organ models, and the designer prosthetics never stop being exciting, but sometimes all it takes to get you to marvel at the capabilities of 3D printing technology is a good old-fashioned drill bit. Or not so old-fashioned, in this case, given that it was manufactured with some pretty new-fangled technology.
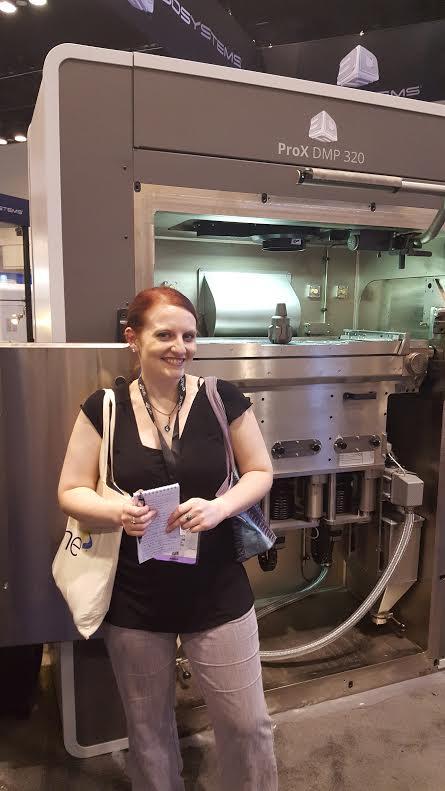
I could totally crawl inside this printer. That’s the 3D printed titanium downhole drill bit behind me – we may have carried it around for a while during our booth tour. #nerds
Last week at RAPID 2016, editor-in-chief Sarah and I were given a tour of 3D Systems‘ booth, which showcased several of the company’s printers, including the recently released ProJet MJP 2500. I was particularly enamored of the also newly-released ProX DMP 320, and I’ll admit that my fascination with it was at least partly because it was large enough to take a nap in. (I did not, in fact, take a nap inside the ProX DMP 320.) We were also able to get a look at some parts printed with the newly introduced printers, and while it’s easy to be impressed with the way a machine looks, it’s a much better indicator of their quality to be able to see what they can do.
A lot of people still think that 3D printing can only make flimsy little plastic things, and while it’s becoming obvious to more people that that’s not true, it’s still hard to get a grasp of the full potential of metal 3D printing until you’ve held a seven-pound 3D printed drill bit in your hand. In my experience of seeing and handling 3D printed objects, I’ve gotten used to things being a lot lighter than they look, and that’s a testament to the technology in itself – one of the hallmarks of 3D printing is the ability to use less material without sacrificing strength. Sometimes, though, you need a part with plain old heft and solidity, and that’s what drew me to the titanium downhole drill bit on display at 3D Systems’s booth.
It turns out that’s exactly what 3D Systems wanted, as they’ve been displaying the part at multiple trade shows as a demonstration of the quality, strength, and surface finish that the DMP 320 can produce. The company recently posted a blog about the 2016 Offshore Technology Conference, which they attended at the beginning of the month and showcased the same technology that they’d brought to RAPID. A demonstration of 3D Systems’ DMP (Direct Metal Printing) Technology was what really got people talking, which isn’t a surprise.
The key to DMP is its ability to print in an extremely low oxygen environment, which allows for superior metal purity in addition to great surface quality. The smooth surface of the drill bit was what really got me – I’m still not used to seeing 3D printed parts that have zero evidence of being printed instead of manufactured in a more traditional way. This particular part was printed by the service bureau 3rd Dimension Industrial 3D Printing, a beta tester for the ProX DMP 320, and according to 3D Systems it was prepped, printed, and post-processed in under 40 hours – a similar part can take up to three months using traditional manufacturing techniques.That’s impressive enough to read about, but it doesn’t really sink in until you’ve seen and held a part with such weight, solidity and overall quality, and thought about the fact that it was printed in about three days – it almost seems like cheating. One of the first articles I wrote for 3DPrint.com was about how expensive and rare metal printers still were. Now metal printing is taking over the industry, and less than a year ago I never would have expected to be getting an up-close look at the technology and what it can produce. I think it’s living up to the hype. Let’s discuss this technology further in the 3D Systems 3D Metal Printer at RAPID 2016 forum over at 3DPB.com.
Subscribe to Our Email Newsletter
Stay up-to-date on all the latest news from the 3D printing industry and receive information and offers from third party vendors.
You May Also Like
Gorilla Sports GE’s First 3D Printed Titanium Cast
How do you help a gorilla with a broken arm? Sounds like the start of a bad joke a zookeeper might tell, but it’s an actual dilemma recently faced by...
Nylon 3D Printed Parts Made More Functional with Coatings & Colors
Parts 3D printed from polyamide (PA, Nylon) 12 using powder bed fusion (PBF) are a mainstay in the additive manufacturing (AM) industry. While post-finishing processes have improved the porosity of...
$25M to Back Sintavia’s Largest Expansion of Metal 3D Printing Capacity Since 2019
Sintavia, the digital manufacturing company specializing in mission-critical parts for strategic sectors, announced a $25 million investment to increase its production capacity, the largest expansion to its operations since 2019....
Velo3D Initiates Public Offering in a Bid to Strengthen Financial Foundations and Drive Future Growth
Velo3D (NYSE: VLD) has been among a number of publicly traded 3D printing firms that have attempted to weather the current macroeconomic climate. After posting a challenging financial report for 2023,...