So often, we see 3D printers used to create some nifty little tool for a tricky little job. Maybe it’s to lock cams together for a timing belt change, or to work as a jig for soldering some complex device. However, some hacks are even simpler than that. [maker_guy] realized that eating nuggets in the car could be easier than ever with a little printed adapter.
The print is simple. It’s a round caddy for the nugget sauces given out by Chick-fil-A restaurants. Why round? Because it lets the nugget sauce sit neatly in your car’s cupholder at an accessible height. Put the sauce tub in the adapter, peel it open, and you can dip to your heart’s content.
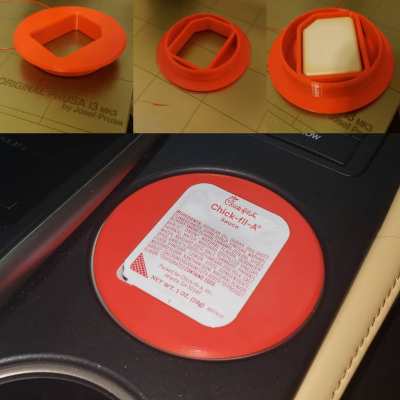
No more delicately balancing Zesty Buffalo by the gearstick while you try and chow down. Nor will your seat covers be tainted with Honey Mustard!
“Not a hack!” you scream. “It’s frivolous nonsense!” To that I say, are you a nugget eater or not? I myself partake, and I can absolutely see the value in this. You see, us journalists work hard. We’re often stuck eating substandard food in our cars on the way from one thing to another, like so many others in busy professions. If a smart little 3D-printed adapter can make mealtime easier and save some mess, I’m calling that a win.
You should never be afraid to use your creativity to make tools to improve your life. Parts are on Thingiverse if you need to print your own. Mod it to suit McDonald’s product if you need. Heck, print in black and it’d look like a stock part of the car!
You don’t have to like this simple adapter, but you can’t deny its utility! Share your own nifty little adapter ideas in the comments.