Under the sea: INL supporting effort to repurpose ocean plastics as blended biofuel feedstocks
Published at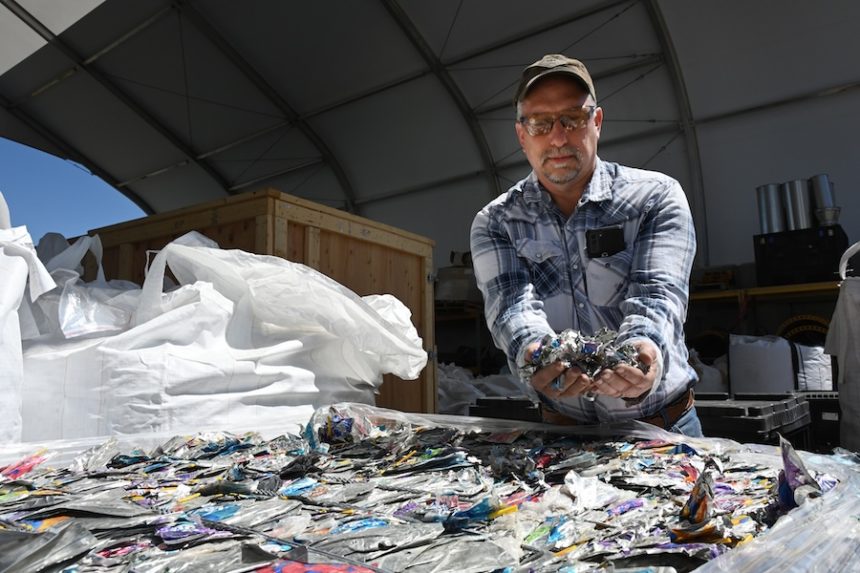
IDAHO FALLS — Perhaps one of the most ubiquitous and powerful images of the ongoing pollution crisis is that of plastic floating in the ocean or littered across once-paradisiacal sandy beaches. The plastic has grown the Great Pacific Garbage Patch, and microplastics found in fish lead to significant health problems and earlier deaths for impacted marine life. These ocean plastics are a sobering reminder of the negative impact humans can have on the world.
Research at Idaho National Laboratory (INL) addresses some of that impact by helping convert these plastics, combined with biomass, into useful fuels and chemicals, using the Biomass Feedstock User Facility (BFNUF). The Ocean Plastics Recovery Project (OPRP), an organization responsible for recovering and reusing ocean plastics, as well as other groups, helped INL acquire a large quantity of ocean plastics to help this effort.
“One of the key benefits of engaging with the Biomass Feedstock National User Facility is the access to modular preprocessing equipment configurations and renowned material-handling experts,” said Luke Williams, a program lead for the facility. “Our partners working on ocean plastics were able to complete a user facility agreement with us to process the plastics using our state-of-the-art equipment and available biomass resources.”
The goal of these user facility agreements is to provide Department of Energy funding to help industry partners conduct feedstock quality research at scales they can’t typically afford alone. These agreements also highlight often overlooked processing research.
Three companies submitted waste streams to INL’s Biomass Feedstock National User Facility (BFNUF) to examine processing strategies that could change the fate of these materials. The plastic waste — including nets, buoys and other debris — washed up on beaches from OPRP. This also included baled Capri Sun pouches, which are 80% plastic and 20% aluminum, from the Alberta Beverage Recycling Company and mixed plastic residues from a plastics recycling facility operated by EFS Plastics.
“One thing we want to understand with these baled drink pouches is whether we’ll be able to recover and recycle that valuable aluminum at the end of the conversion process,” Williams said. BFNUF researchers will study how multilayered packaging impacts gasification processes and if the aluminum can be recovered from the plastic.
BFNUF’s role is to process material into an optimal shape, size, density and moisture content, while also removing contaminants like ash and halogens that will allow the material to be most efficiently converted into biofuel. The team learned many lessons from breaking down and reshaping the ocean plastics, largely due to the diversity of materials.
Initial pelletizing tests with ocean plastics created high-quality pellets. Later tests, however, created a melted mass that plugged the machine. The melting was probably caused by the ground fishing nets that made everything tangle and clog. The BFNUF team innovated by adding mixed biomass — in this case, roughly 20% ground pine by mass — to keep material moving and to provide a porous surface to bind with the plastics.
Adding the wood chips made this new feedstock partially bio-renewable and improved pellet durability through greater binding of the mixed materials.
“One of the biggest challenges with such diverse wastes is separation of contaminants and consistency of flow after size reduction,” Williams said. “Because plastics that have washed up on beaches include items like large buoys, tarps and fishnets, they are much harder to break down into a consistently flowable material.”
While most of the material was processed into a pellet form, Williams noted that the drink pouches were cubed, and that the cubes also broke down into flakes with heavy processing. BFNUF researchers have not had many opportunities to analyze how flaky material passes through standard feed handling systems. This is one of the issues they hope to better understand during the conversion process from biomass pellets to biofuels, which uses a variety of equipment. They also plan to explore how some of the plastics and biomass blends, which were prepared using small amounts of a chlorine-rich packaging film, would impact conversion performance.
The researchers have gained valuable insights into turning ocean plastics into a flowable feedstock. Those insights include how to break down new materials with sometimes unknown compositions and how to blend waste with biomass to solve flowability challenges. Now, they are better equipped to deal with heterogeneous materials and compounds, which will be crucial in the fight against environmental pollution. However, the BFNUF team still has a lot to learn about how these ocean plastics and other mixed wastes will respond to the conversion process to produce useful fuels and chemicals.
“While some material discarded on beaches can be sorted out and recycled, it’s important to have a place and use for the pieces that would otherwise contaminate our environment and contribute to microplastic pollution,” Williams said. “Taking these harmfully discarded plastics and turning them into fuels and chemicals is a key part of the BFNUF mission.”