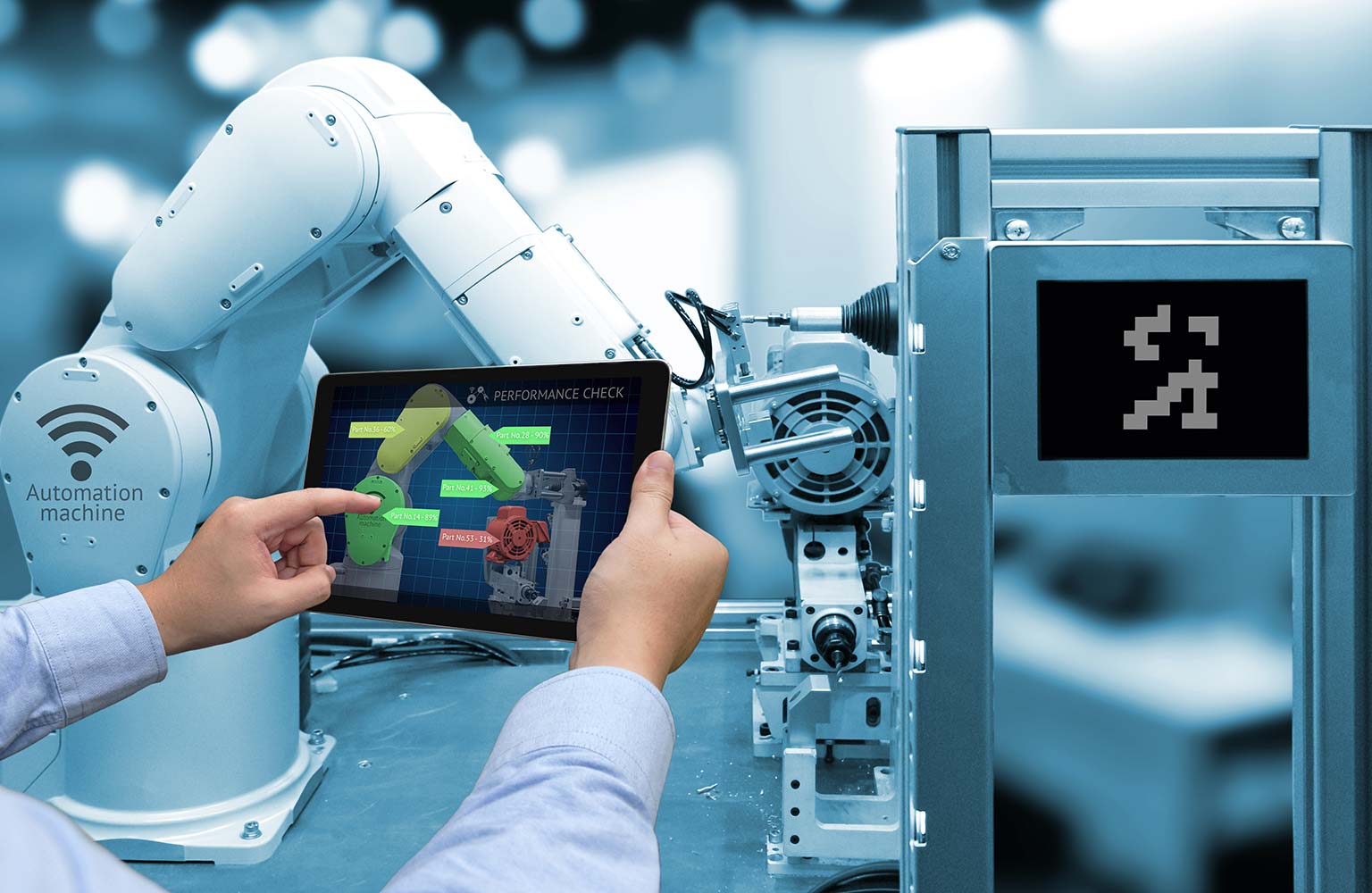
Build: Technology is advancing the ways we create, and experience, our spaces
Powering the Smart Factory with the Internet of Things
To secure a smart future, manufacturers are leveraging the Internet of Things to reshape product development and production. Selecting the right infrastructure is crucial for success.
The first half of the digital revolution was about using machines to connect people—allowing them to share ideas, experiences, memories, and more with others halfway across the globe
The second half will be about enabling machines to talk to each other, using cloud-connected Internet of Things (IoT) devices to help automate the creation and delivery of products.
Manufacturers are bullish in their assessment of IoT’s potential. For example, 67 percent of companies in the industrial manufacturing sector have an ongoing smart factory initiative. In a smart factory, previously disparate systems and devices become connected so the stream of data they produce can be turned into actionable insights.
Exploring what happens when possibility becomes reality.
Most of IoT’s value will likely come from its ability to optimize operations. But IoT has the power to radically reshape every aspect of product development and delivery, from the plant floor to the value chain:
- Machine sensors allow factories to measure and reduce energy and water waste, leading to lower costs and environmentally sustainable operations.
- Manufacturers can feed information from other systems and devices directly back into the production line, enabling them to make improvements in days or even hours.
- Better asset tracking and sensor-based alerts trigger orders when stock runs low, allowing manufacturers to completely automate the inventory replenishment process.
- Manufacturers can automatically identify potential equipment failures before they happen, protecting employees and minimizing unplanned downtime.
“It’s an expectation now that the IoT will fundamentally change not only the computer industry, but also society,” says Greg Bollella, VMware vice president in the office of the CTO. “The IoT will be a significant driver of what’s coming to be known as ‘the fourth industrial revolution.’”
The Right Infrastructure Required
The possible applications of IoT in manufacturing are almost endless—once the right infrastructure is in the place. And therein lies the challenge.
In the past, operational technology (OT) and information technology (IT) were separate domains, staffed by experts with limited knowledge and understanding of their counterpart’s requirements. However, the successful implementation of IoT demands that this siloed approach be dismantled and replaced with a unified infrastructure that treats the different elements of OT and IT as complementary cogs within the same process wheel.
Moreover, security becomes a more important issue for both OT and IT. If the multitudes of connected devices and systems are not secured properly, hackers, hostile governments, and competitors can gain access to sensitive information or disrupt operations. As a result, manufacturers need to build an infrastructure that closes the gap between OT and IT, while minimizing security risks.
“The proliferation of IoT gateways and IoT-enabled cyber-physical systems present huge security and management challenges,” Bollella says. “We believe that ultimately IT organizations and professionals will be asked to manage, secure, and maintain the infrastructure underlying many of these IoT solutions.”
Making Unplanned Downtime History
From an operational perspective, downtime has always been enemy number one. IoT helps manufacturers minimize downtime by providing real-time visibility over the status of every machine in the factory. But that’s not all.
Once the machines are connected to a single management platform, machine failure parameters can be continuously measured and analyzed. Based on these parameters, normal and abnormal states can be tracked much more accurately. This allows manufacturers to take preventative action before problems occur, thus saving time and money by minimizing damage and disruption.
Patterns eventually emerge from all the data that’s being collected and analyzed. These patterns can be fed back quickly into the manufacturing process, helping improve the effectiveness of future manufacturing and maintenance processes and optimize future machine and component purchases. German manufacturer Bosch has put IoT to work in its own facilities, such as the Bavarian factory where it builds braking and safety systems for nearly 7 million cars each year. Using connected devices on the shop floor has enabled company engineers to reduce error rates and boost productivity by up to 24 percent.
Securing an Expanded Attack Surface
Traditionally, factories have been primarily closed systems, so securing them against Internet-based attacks was not a significant priority. To minimize any operational disruption from potential vulnerabilities, many OT systems were walled off from IT.
Today, this siloed approach hinders the implementation of IoT in the factory. That’s because effective IoT implementations require greater OT and IT integration and more connections to external or third-party data sources, systems, and analytics platforms.
Building a smart factory requires a thoroughly connected, integrated infrastructure. But connecting machines directly or indirectly to the Internet, or even to a private cloud environment, significantly enlarges the potential attack surface area. That means more access points criminals could exploit for espionage, vandalism, or terrorism. Risks include machine damage, factory worker injury, intellectual property theft, and production or supply chain disruption.
What’s needed is a reliable platform for the secure, integrated management of IoT within factories. It should be able to distribute software upgrades and security patches to devices and edge systems at scale, and rapidly quarantine rogue devices if a breach or other anomaly is detected.
“At VMware, we are readily embracing these fundamental challenges presented by IoT,” Bollella says. “We are building a suite of management and security technologies that, from their inception, address IoT security and management challenges.”
Enabling the Connected Supply Chain
In a smart factory, production processes can be directly connected to supplier, logistics, product lifecycle, and ordering systems. As a result, manufacturers can more easily accommodate rapidly changing and increasingly individual customer requirements.
Consider the process of ordering a new kitchen. In the pre-IoT world, you have to manually select the specifications and components in advance. Once the order has entered the vendor’s system, you’re basically out of luck if you want to make any changes.
Now let’s look at a truly connected manufacturing process. If you want to change the color and other specifications of the oven you ordered, the vendor can inform the relevant production line immediately to adjust the processes required to execute the changes. And the systems for managing stock levels and invoicing would also be updated as part of an automated, IoT-enabled process.
Increased integration can deliver similar benefits across the supply chain. For example, the ability to use better asset tracking and inventory management allows manufacturers to optimize costs by reducing asset loss and “empty shelf” incidences. Or an IoT-enabled vehicle fleet can adjust employee transport and product delivery routes according to weather conditions, traffic congestion, and other variables.
A centralized, integrated IoT platform lets manufacturers control the entire supply chain, enabling every “thing”—whether a component shipment, product, or a warehouse vehicle—to be managed securely and accurately from a single console.
Making the Factory of the Future Real—Today
When people talk about how IoT will impact manufacturing, they’re really talking about taking massive amounts of data produced every day by connected devices, and then applying artificial intelligence to uncover hidden patterns and glean new insights.
An end-to-end infrastructure management system, such as VMware Pulse IoT Center, allows manufacturers to deliver relevant data where and when it’s needed across the edge and in the cloud by integrating into enterprise systems. It enables efficient, secure operation of manufacturing processes and the supply chain that feeds them. Offering IoT-engineered solutions like these, says Bollella, enables VMware to serve as a strategic partner to companies in their IoT journey.
As a result, smart factories will allow manufacturers to mass-produce more goods at lower costs and with fewer defects. And they’ll increasingly be used to create products customized for each individual, as we move toward a personalized, data-driven future.
The Possibility Report is an ongoing series about how technology is changing our understanding of the world around us. This article is part of BUILD, our discussion on how emerging technologies promise to change the way we design, create, and experience the places we live and work, from city centers to the remote villages of tomorrow.