IC bonding technique shrinks encoder design
August 19, 2002
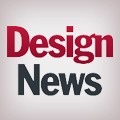
Recent developments in semiconductor design and bonding techniques that help engineers arrange electronic components in very small spaces let Heidenhain Corp. set new size standards for true absolute rotary encoders. In fact, its genuine absolute multiturn encoder, the EQN 1125, measures just 36.5 mm in diameter and 39 mm in length. Previously, the company's smallest true absolute encoder was in a 58-mm diameter package.
|
The launch of this small absolute encoder with real gears couldn't be timelier. So-called absolute encoders that rely on battery-backed electronic revolution counters require maintenance, and are susceptible to interfering signals and battery failure. And as smaller three-phase servomotors keep moving into more applications, the need for absolute position value, at start-up or after power interruptions, is increasing in areas such as robotics, handling equipment, and assembly automation.
To draw a comparison, when incremental encoders lose power, they also lose positional information and require a reset or homing cycle to synchronize with the control device. In addition, they only keep track of position within one revolution. Absolute encoders, in contrast, eliminate the need for homing cycles or reference mark runs by keeping track of the number of revolutions as well as the position within each single turn of the encoder.
Providing a unique signal for each position immediately on power-up means faster and safer start-ups. Absolute encoders can also improve tolerance to disturbances, contribute to greater accuracy and repeatability require zero maintenance, as well as provide more compact designs.
For example, in robotic applications absolute feedback can contribute to more compact assembly cell designs if homing a robot involves extending its arm to its maximum reach. In such a case, the robot is cell would have to be larger than the process dictates just to accommodate the reset cycle. With absolute encoders engineers could design the assembly cell more tightly around the robot and the parts that it's handling, saving floor space in the process.
|
True absolute encoders, according to Heidenhain Manager Tom Wyatt, need no electronic counter or battery backup. Instead, Hall effect sensors detect the position of three magnets rotating on the gearing arrangement to ascertain the number of revolutions. The EQN 1125's size enables servomotor frame sizes of 40 mm to be equipped with absolute rotary encoders, according to Wyatt. Because smaller servomotors generally run hotter, the encoder is designed for use in temperatures up to 115C (239F) and is mechanically interchangeable with the corresponding incremental encoders of the ERN 1100 series.
Chip-On-Board (COB) technology was key to getting down to this size. The design and bonding technique eliminates traditional circuit board connectors and soldering of integrated circuit housings on a board, according to Wyatt. Rather, COB applies the "naked" chip to the board. Once electrically contacted, the chip is encapsulated for protection. "COB saves space because all the electronics fit on one board," explains Wyatt. "Moreover, the elimination of solder connections reduces the number of contacts by one half, to improve encoder reliability."
For this application, Heidenhain developed all electronic components for scanning and signal processing with the ultimate goal of reducing size and number of components and connections. The OPTO-ASIC (Application Specific Integrated Circuit) and digital and mixed-signal components are all application specific, says Wyatt. For example, the ASIC, not only has integrated photosensitive scanning surfaces, but includes the EnDat bi-directional serial interface and a mixed-signal processor as well.
|
"The built-in photo cells reduce the size and the number of discrete components, and the processor does a quick comparison of the incremental portion to the absolute portion before sending the out-put via EnDat to subsequent electronics to ensure good output on both sides," according to Wyatt. EnDat is Heindenhain's bi-directional interface for absolute and incremental encoders.
Because COB uses wire connections between chip and the board that are only half as thick as a human hair, special clean room facilities are required for production. "The small, 0.001-inch diameter wires are susceptible to airborne liquid and particle contamination, so production of both COB and SMD assembly is done in a clean room to guarantee consistently high operator independent quality," says Wyatt.
EQN 1125 Specifications |
---|
Source: Heidenhain Corp. |
Absolute position values EnDat interface: |
4,096 distinguishable revolutions |
Incremental signals: |
Accuracy: |
Power supply: |
Maximum consumption: |
OEM memory area: |
Vibration stability: |
Operating temperature range: |
Permissible speed |
Dimensions |
Contains position deviation within one revolution and within one signal period, and is guaranteed when within the mounting tolerances |
Additional Details |
Contact Tom Wyatt, Heidenhain Corp., 333 E. State Pkwy., Schaumburg, IL 60173-5337; Tel: (847) 884-3713; Fax: (847) 490-3931; E-mail: [email protected]; www.heidenhain.com or Enter 501. |
About the Author(s)
You May Also Like