Problem-solving piezoelectrics
September 23, 2002
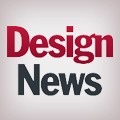
Even now, piezoelectric phenomena-discovered by Pierre and Jacques Curie more than 120 years ago-remain something of a laboratory curiosity. Despite their distinguished service record in applications such as ultrasonic transducers, microphones, and accelerometers, piezoelectric products are just beginning to penetrate the wider marketplace, as the following examples attest
Rotary torque transducer
|
While resistive strain gauges are the dominant technique for measuring static as well as dynamic strain, translation to non-stationary applications such as rotary shafts requires expensive slip rings or large low-frequency transformers.
Torqsense(TM) transducers present an alternative method for measuring strain, and therefore, torque. Developed by Sensor Technology Ltd., the patented transducer correlates velocity and attenuation of surface acoustic waves-SAW, also known as Rayleigh waves-with residual stresses in the surface layer of a piezoelectric substrate attached to the material stressed.
To work, two comb-shaped arrays-metallic film transducers fabricated from standard IC technologies-are layered onto one end of the piezoelectric substrate. Passing a high-frequency voltage across the arrays generates a periodic undulation of the piezoelectric substrate to produce the waves. A similar 'receiving' terminal at the other end of the transducer converts the waves back to an electric signal.
|
Wave propagation is at right angles to the comb array's interleaving electrodes. Strain, consequently, will change electrode spacing, altering operating frequency. Two SAW transducers bonded at 45 degrees to the longitudinal axis and connected in a half bridge configuration measure torque in a shaft. When the shaft is strained, the difference in frequency output between the transducers relates to the applied torque.
An electromagnetic coupling device comprising two concentric hoops, one fixed to the shaft housing, the other to the rotating shaft, provide non-contacting interrogation. Other benefits include low cost, minimal shaft length, low inertia, high bandwidth, and signal immunity. Torquesense transducers are available in seven sizes measuring torque from 100 mNm to 10,000 Nm at full-scale deflection with smaller ranges having speeds to 30,000 rpm. For a white paper on SAW transducers, visit this story at www.globaldn.com.
For more information: Sensor Technology Ltd., Banbury, Oxon, England: Tel: +44 1 295 730 746; [email protected]; www.sensors.co.uk, or enter 554
Piezo-operated valves
Ethanol fumes-volatile and flammable-make the blending and bottling of spirits and liqueurs tricky. Consequently, when Allied Distillers were modernizing its plant at Dumbarton in Scotland, they needed to install intrinsically safe equipment, opting for an electrical system based on the Sensoplex 2 safety fieldbus. Conventional solenoid-operated valves were ruled out for flow-control duties due to concerns about the large amounts of power they would need from the bus. Instead, the new system uses low-power piezoelectric actuators from Hoerbiger-Origa to control the flow of numerous products throughout the plant.
|
In the old system, valves controlled by a compressed air signaling system routed the various products along the pipes throughout the plant. With many kilometers of six millimeter piping, the system was slow in response and inflexible when modifications were required. Hoerbiger-Origa's piezo-technology, in contrast, features a simple three-port, two-position valve in which a piezoelectric element switches the airflow. Operating like a bimetallic strip, the piezo element deflects in direct proportion to an applied voltage, so that the valve may either be used in a simple on/off switching function, or in a proportional mode, to produce an analog pressure output. Response time is typically less than two msec and the circuit protection normally associated with solenoid valves is not needed.
Thirteen four-channel safety fieldbus subsystems comprise the overall control system. Each channel controls 256 inputs/outputs (I/O), providing plenty of flexibility for future changes and developments. The modernized plant employs more than 400 Hoerbiger-Origa piezo units.
For more information: Hoerbiger-Origa Corp., Glendale Heights, IL, USA; Tel: (630) 871-8300; [email protected]; www.hoerbiger-origa.com; or enter 555
Low-power door lock
Electronic door locks usually make use of conventional solenoids to provide the actual bolt locking mechanism. However, this method is inefficient because it requires continuous current to activate the solenoid, it generates heat, and needs shielding from interference.
|
Applying their Servocell piezo-actuator technology to this problem, PBT produces a low-power strike-plate mechanism for electrically operated locks. The actuator requires 90-96% less power than conventional designs, making battery-powered electronic door locks a viable option. Due to the low current, control level signals can be used to operate the actuator, enabling operation directly from fieldbus systems.
In the past, piezoelectric devices required about one KV per mm thickness of the ceramic crystal. The ceramic was brittle and unsuitable for sustained, heavy-duty applications. In addition, the range of movement proved insufficient for low-cost manufacturing processes. Conventional higher-specification piezoceramic devices often incorporate rare-earth metals and need adjustment to compensate for manufacturing tolerances-all factors rendering them too expensive for general applications.
The Servocell addresses these problems, meeting engineers' demands for a more application-friendly piezo-actuator. The actuator is based on the planar bimorph process, patented by PBT. This configuration consists of a U-shape with two diametrically opposed ceramic elements. Versions with three or four prongs are possible to give a higher force or a larger range of movement. Once fixed onto frames, the actuators can be conveniently mounted into applications with the frame providing easy handling and simple power connection.
Paul Jones, of Servocell Marketing, remarks that the technology is also applicable to machine interlocks.
For more information: PBT Ltd., Harlow, Essex, England; Tel: +44 1279 621500; [email protected]; or enter 556
Nanoliter dispenser
Engineers at Olympus Optical Co. and Yamagata University joined forces to take advantage of the related concepts of motion and inertia in developing a new nozzle for depositing nanoliter volumes of fluids. Their nozzle has a cylindrical piezoelectric element measuring 2mm in diameter and 1cm long with a glass capillary threaded through the cylinder and fixed at the leading end. At the back end of the glass capillary is an elastic sealing piston.
|
The piezoelectric element is polarized so that a voltage causes the cylinder to contract along its length. Any contraction pulls the glass capillary sharply, though a minute distance, toward the sealing piston. Because of the inertia of the fluid, a droplet will squirt out of the capillary nose. Laser strobe photography verifies that droplet volume increases linearly with increasing drive voltage and can be controlled to eject from 0.4 to 1.5 nanoliters of fluid.
Olympus believes the new nozzle could be put to use in biomedical applications, such as preparing DNA microarrays, or in various screening tests that require manipulating trace amounts of fluids. An Olympus engineer says their nozzle promises several advantages over the approach used in inkjet-like nozzles. Inkjet nozzles typically rely either on heat or on piezoelectric deformation of a reservoir to push fluid from the nozzle. The use of heat is not appropriate for many biological fluids and piezoelectric deformation requires that the assembly be glued together.
The new Olympus nozzle relies simply on movement and inertia. This means the piezoelectric element and the glass capillary can be screwed together and more freely assembled and disassembled. If the capillary is damaged, that part alone can be replaced. He says the device should be able to achieve greater precision in both positioning the ejected fluid and in controlling the amount. However, further development work is needed and the company has not yet confirmed plans for commercialization.
For more information: Olympus America Inc., Melville, NY, USA; Tel: (800) 645-8160; www.olympusamerica.com; or enter 557
Spherical motor
Shigeki Toyama, an engineer at Tokyo University of Agriculture and Technology, has put three piezoelectric elements to work in harmony. The result is a unique actuator that he expects to be used in robotic arms and to control the movement of security cameras, among other applications.
Operation is simplicity itself. Three discs hold a small sphere in place; each disc incorporates a piezoelectric element. Applying a voltage to the element induces an ultrasonic vibration. By controlling the amount and polarity of the voltage applied to each element, the rotation of the sphere can be controlled so that it will rotate in virtually any direction. If a shaft or other assembly is attached to the sphere, travel is limited only to avoid hitting the discs. Current robotic arms require complex joints to achieve the same 3 degrees of freedom.
The prototype motor developed by Toyama and his team incorporates a 45-mm diameter sphere and weighs only 195g but develops a drive torque of 1.5 cm-kgf and a holding torque of 3 cm-kgf. Maximum speed is 2 revolutions per second. The motor does not generate nor is influenced by a magnetic field. It also responds quickly, does not need a braking mechanism and holds the sphere in position even after the drive voltage is cut off.
Toyama believes that when mass-produced, the motor could cost as little as $50 U.S. Toyama patented the new motor by himself, and will license the technology through the university's technology licensing office. He says he has reached an agreement with one major Japanese precision manufacturer who is now gearing up to mass-produce the motors, though he declines to disclose which one. His team has already used the motor for the joints of a robotic arm and to control a prototype security camera. He adds that they have received inquiries from factory automation firms as well as toy makers.
For more information: Shigeki Toyama, Tokyo University of Agriculture and Technology; Tokyo, Japan; Tel: +81 423 88 7097; [email protected]; or enter 558
Shock sensor
Most piezoelectric devices take advantage of the material's ability to deform when subjected to an electrical charge. Murata Manufacturing Co. has turned this principle around, using the electrical charge produced by deformation as the basis for a tiny shock sensor. The new sensor uses a piezoelectric element that spans a cavity in a housing. The element is like a beam, supported at both ends, and is a bimorph, consisting of two layers of piezoelectric ceramic crystals cemented together to increase the charge from a given stress. Any acceleration of the sensor results in the deformation of the piezoelectric beam and the subsequent generation of an electric charge that is proportional to the stress of deformation.
Murata had previously used this approach in voltage-sensitive detectors. But the company claims that using charge-sensitive detection makes their new sensor twice as sensitive for a given size. And because the new sensor uses a peripheral amplification circuit, sensor wiring impedance is low, minimizing the effects of external noise. As a result, its signal-to-noise ratio is better than that of a conventional voltage-sensitive type. The new sensor also withstands temperatures up to 260C, allowing for reflow-soldering, another advantage over voltage-sensitive models.
Intended use: hard disk drives. If a hard disk drive is jostled while writing data, the head can lose its place and overwrite data on an adjacent track. To prevent this, most disk drives have sensors to detect shocks and circuits that suspend writing until the head can be returned to the correct position. Such countermeasures have become increasingly important with increases in disk data density. Murata believes the small size of their new sensor, which is about two-thirds of current comparable sensors, will be ideal for use in 2.5-inch hard disk drives. They can also be used to control CD-ROM rotation speed and in the feed-forward control of optical pickups for such devices as DVD players. The company has not disclosed prices but says the new sensors cost less than existing models.
For more information: Murata Electronics North America Inc., Smyrna, GA, USA; Tel: (770) 436-1300; www.murata-northamerica.com; or enter 559
Optical switch
Mitsubishi Electric Corp. engineers have turned to piezoelectric elements in designing a mechanical optical switch the company believes will be at the heart of new-generation large- capacity all-optical communications systems.
|
In the new optical switch, waveguides that serve to direct the path of the light signals are formed in a 32-by-32 grid pattern within a polymeric substrate. Tiny slits, cut into the substrate at the intersection of each waveguide, slice through the waveguides at a 45-degree angle. The substrate sandwiches between two resin plates having holes aligned with the waveguide intersections. Piezoelectric elements are placed so as to extend into the holes and make contact with the polymeric waveguide.
When an optical signal is intended to travel through a switch, the piezoelectric elements keep the waveguide in its flat position. In this condition, it is as if there were no slit through the waveguides and the signal travels straight across the junction. Charging the piezoelectric elements pushes the waveguide up to redirect a signal. This opens the slit, creating an air gap that results in the optical signal being reflected 90 degrees into the intersecting waveguide.
Mitsubishi says they selected a piezoelectric driver because of its fast response, precise movement, and low power consumption. And, while the prototype Mitsubishi has used to prove the principle has a 32-by-32 grid of waveguides, the company believes this could easily be scaled up to boost switch capacity. Mitsubishi is presently developing an optical signal router that plans to be able to handle hundreds of gigabits per second. Even more importantly, Mitsubishi claims the new switches can be produced at one-third of the cost required to manufacture optical switches based on alternative operating principles.
For more information: Mitsubishi Electric and Electronics USA Inc., Cypress, CA, USA; Tel: (714) 220-2500; www.mitsubishielectric.com; or enter 560
Nanometer motion control
Each of the vibrating elements that comprise this ultrasonic piezomotor exhibits two natural frequencies. One frequency causes elongation; the other frequency, bending. Simultaneous excitation of both modes results in an elliptical motion at the element tips.
Because the piezoceramic elements are spring loaded against a ceramic strip fixed to a carriage, friction from the oscillating elements pushes the carriage in one direction. The higher the excitation voltage, the faster the carriage moves. Phase shift between excitation modes determines carriage direction, while the number of elements dictates available power. Patented by Nanomotion Ltd., the motor offers a number of benefits including small size, the ability to operate in high vacuum, and a velocity range from less than one micron per second to 25 cm per second. In addition, Nanomotion motors do not generate, and are not influenced by, magnetic fields.
|
A closed-loop servo controller developed by Nyquist Industrial Control makes the motor even more attractive. Employing piezo-specific algorithms from Nanomotion, the controller overcomes the motor's non-linear behavior due to slip caused by variations in friction force. Firmware features include antifriction offset, a dead-zone algorithm, velocity feed forward, and ultra high resolution. On the hardware side, the controller offers a high servo rate (greater or equal to 10 KHz), PID (Proportional-Integrated-Derivative) control to minimize position error, and a wide dynamic range of command (+ and -10 Bit). As a result, the Nyquist controller is fully capable of driving the Nanomotion motor to its full potential.
For more information: Nanomotion Inc, Ronkonkoma, NY, USA; Tel: (631) 585-3000; [email protected]; www.nanomotion.com; or enter 561
Nyquist Industrial Control; Eindhoven, The Netherlands; Tel: +31 40 257 88 88; [email protected]; www.nyquist.com; or enter 562
Big theater sound
Thanks to new "home theater systems," there has been a resurgence of interest in active control for loudspeaker cones. This is especially true for sub-woofers designed to accurately reproduce earthquakes, explosions, and other movie sound effects not normally encountered in conventional music recordings. The "Komri" speaker system from Linn Products Ltd. (www.linn.co.uk) employs a piezoelectric accelerometer to not only extend the loudspeaker's low-frequency response, but eliminate distortion as well.
Bill Miller, design engineering manager at Linn Products explains that an ideal speaker will exhibit flat frequency response characteristics extending down to the limits of the audio band. For home theater, this may be as low as 15 Hz. Distortion-free audio reproduction, he adds, requires that a pure sine wave reproduced at a given frequency creates an acoustic pressure wave of identical shape, without harmonic components or non-linearity. This, however, is not easily accomplished, given that speaker motion is created by magnetic effects that may become non-linear at high amplitudes.
Because it is immune to magnetic as well as electrical or pressure fields, and since sound pressure level created by the cone (as a function of drive current) is proportional to cone acceleration, the ACH-01-03 piezoelectric accelerometer from Measurement Specialties Inc. has proven itself good for the task. Weighing just 4g, it offers a dynamic range suitable for operation to about plus or minus 150g, and it introduces minimal electrical noise into the control loop, especially at low frequencies. Since the error compensation signal fed back to the input is derived from the difference between the "ideal" signal and the accelerometer output, any extraneous source of noise would be fed back and amplified, and could become audible.
Assembly is easy. The device has a flat base suitable for adhesive mounting onto Linn's custom built driver. In addition, the accelerometer features built-in impedance-matching circuitry and an integral shielded cable that passes through the cone to the amplifier and control electronics.
"Although the sensor has a bandwidth that extends beyond the upper limit of the audio band," notes Richard Brown of Measurement Specialties Sensors Products Division in Germany, "the control signal is primarily of use at low frequencies only, where the uncompensated subwoofer driver deviates from ideal behavior. Response, therefore, is rolled off at around 200 Hz." Appropriate gain and phase response within the loop, he says, allows the sound pressure level to show flat frequency response down to 15 Hz (-3 dB). To achieve adequate peak levels, the sub-woofer delivers a maximum excursion of plus or minus 12.5 mm. Peak drive current from the controlled power amplifier is around 20A, for a 1,400W peak power delivery.
"It is really remarkable," Brown points out, "to simply touch the cone before and after the control loop is enabled. Without active control, the cone deflects inwards easily, and recovers position in a 'relaxed' way when finger pressure is released. With the control loop active," he notes, "the cone feels like a brick wall, pushing back with surprising force."
For more information: Measurement Specialties, Inc.; Valley Forge, PA; Tel: (610) 650-1500; www.msiusa.com; or enter 573
About the Author(s)
You May Also Like