Cloning Musical Heritage In The Key Of 3D
When Mina Jang played the same melodious tune on two different flutes behind a screen, she said the examiners grading her couldn't tell the difference.
Yet the two instruments were made in dramatically different ways.
One was a handmade version of an original early 18th-century flute crafted in 2001, while the other was made of white plastic and "cloned" using a 3D printer in 2019.
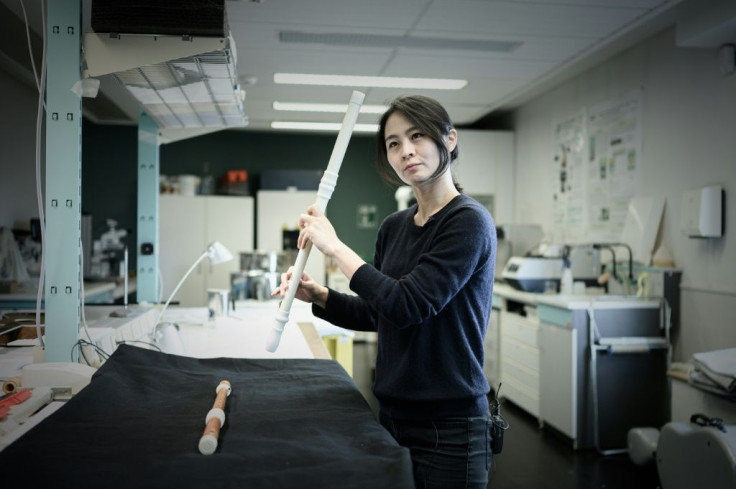
The Museum of Music in Paris, whose collection includes a 2,500-year-old flute made of a vulture bone, has recently begun experimenting with the technique in an effort to better preserve period instruments.
"The idea was to find out how to rapidly obtain a copy of an instrument whilst respecting the original flute," said the 35-year-old professional flautist and researcher in baroque music, who initiated the idea.
Before being printed, the carefully copied 18th-century flute was x-rayed to identify its precise characteristics.
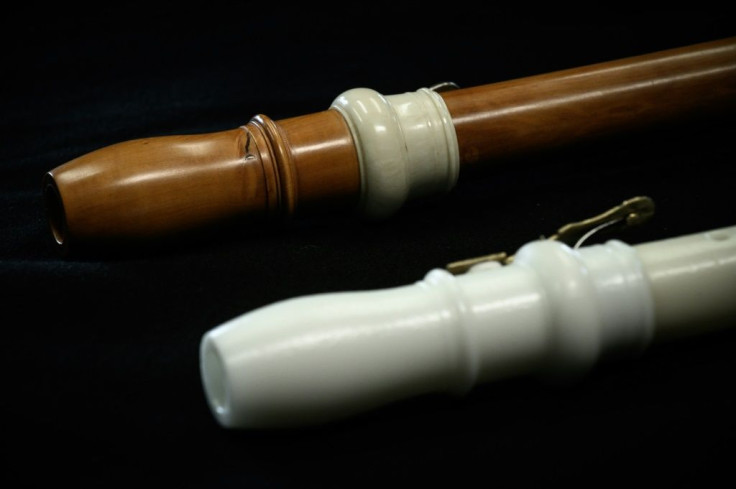
The original it was based on was made by the celebrated French composer and instrument maker Jacques-Martin Hotteterre and is today preserved behind glass at the museum.
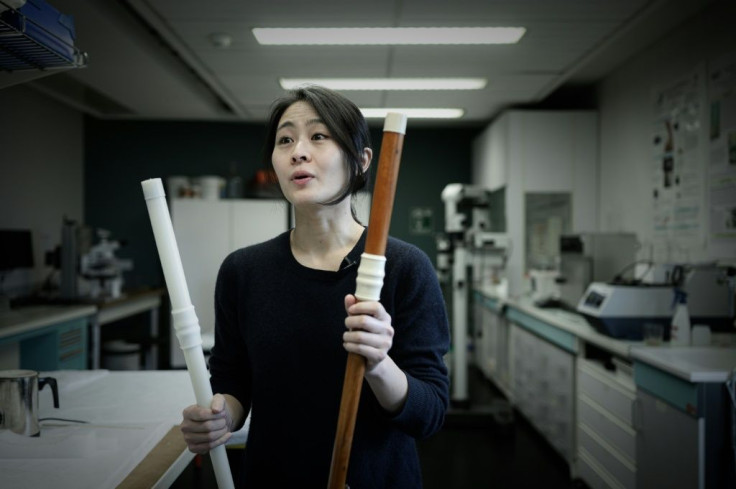
3D printing has advantages over handmade instruments, taking just 24 hours to make, compared to a month in a workshop, and costing hundreds instead of thousands of euros.
But Stephane Vaiedelich, in charge of the museum's laboratory which worked with other partners on the project too, says the move is purely about conserving musical heritage.
"3D printing isn't about replacing instrument makers," he told AFP.
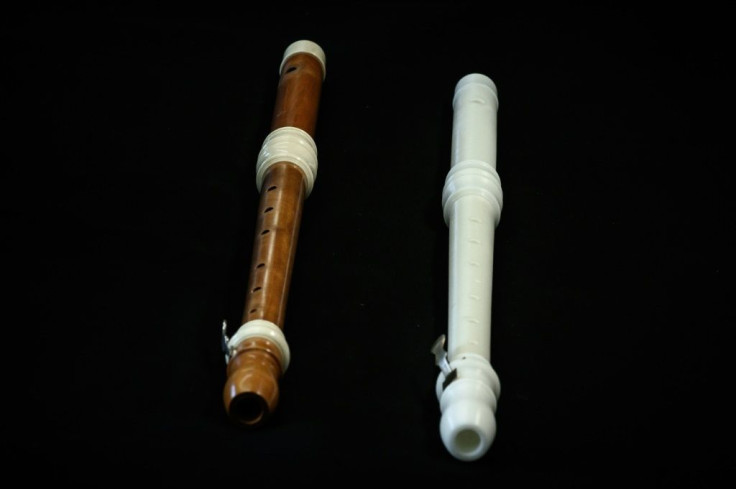
"The idea is to recreate a historical instrument so that the public can appreciate its sound and to revive an important heritage.
"It's an extraordinary way of travelling through time and recapturing old repertoires," he said, adding that a second flute had also been cloned.
While 3D printing has become increasingly popular in different sectors over the last 20 years, including for reproducing instruments, Vaiedelich said the museum believed it was the first to experiment with the 3D reproduction of old instruments, using a scientific approach.

A few orchestras play using original instruments from the period, such as the French group Les Siecles (The Centuries), but wind instruments struggle to withstand humidity.
"It expands wood and can break" the instruments, Vaiedelich said.
The museum chose to copy a transverse flute, precisely because -- unlike an oboe -- most of the musician's breath passes outside the instrument.
"The material has less of an impact on the timbre," Vaiedelich said.
Using plastic for the 3D reproduced instruments also raises environmental issues. Vaiedelich said the ideal would be to print using recycled materials.
Fanny Reyre Menard, vice-president of the trade union grouping together makers and repairers of instruments, said the material used was the only downside.
"For craftsmen, plastic cannot be compared to wood," she said.
"A wooden sound box is fundamental for a violin."
On the whole though, Menard said that 3D printing presented an opportunity.
"It's not a danger, but rather a very good tool for sharing information and prototypes between craftsmen," she said.
"Some parts are improved when adapted, for example chin rests for violins or mouthpieces on wind instruments," said Menard.
"If I find a form that interests me, I send a file to a colleague and he prints it. It's great."
ram/ech/kjm
© Copyright AFP 2024. All rights reserved.