Recycling in Additive Manufacturing: Coming Full Circle with End-of-Life Glass Fiber Reinforced Composites
In the recently published ‘Remanufacturing of end-of-life glass-fiber reinforced composites via UV-assisted 3D printing,’ authors Andrea Mantelli, Marinella Levi, Stefano Turri, and Raffaella Suriano, from Politecnico di Milano, opened a study to investigate the potential of 3D printing for end-of-life (EoL) composites.
Their expectations of this work are environmentally sustainable structures that can be created affordably and fast, with complex geometries and suitable mechanical properties. Suggested applications are street furniture and urban renewal—all for a ‘circular economy model.’ The researchers delve deeper into the topic of recycling in 3D printing; and while it may sometimes be a complex procedure, it is critical due to the large amounts of materials being discarded whether at the end of their usefulness or considered waste after a failed print.
Pointing out that fiber-reinforced polymers are a ‘peculiar class of engineering materials,’ the researchers are aware of the challenges in recycling—in comparison to thermoplastics, richer in nature due to multiple materials. Because ever-increasing amounts of this composite waste are reaching the end-of-life (EoL), it is critical now to find better ways to recycle, rather than dumping these parts into landfills. Ultimately, what the researchers would like to see is a movement away from ‘take, make, and dispose,’ and one toward ‘reusing, recycling, repairing, and remanufacturing.’
In most programs today, the costs of recycling outweigh the advantages—and especially with glass fiber reinforced composites (GFRCs). These materials can in some cases be recycled via grinding, splitting, or hot and/or cold crushing and forming. Recycled glass fibers can also be used as fillers. The researchers also state the potential for using waste polymers to make filament.
“Very recently, continuous carbon fiber reinforced thermoplastic composites have been recycled and remanufactured by means of fused deposition modeling (FDM) technology,” state the researchers.
Here, they experimented with the 3D printing of GFRCs to explore the efficacy in reusing shredded solid recyclates.
The research team noted the best success in printing with the composition 20D45R as the object produced was ‘flawless.’ They were able to modify their 3D printer, adding a third UV-LED and specific support for these features.
“In an LDM-based printing process, the study of the rheological behavior of printable inks is crucial because ink viscosity influences its flow through the extrusion nozzle, hence, affecting the printability of extruded inks and the possibility to obtain three-dimensional objects,” stated the researchers. “To analyze the rheological behavior of different printable inks, several compositions were investigated at varying the percentage of the reactive diluent and recycled GFRCs.”
The 3D printed composites exhibited good surface quality, although samples did show elongation at break which was ‘slightly higher’ than the printed composites. It was suspected this may be due to defects in the composite samples themselves.
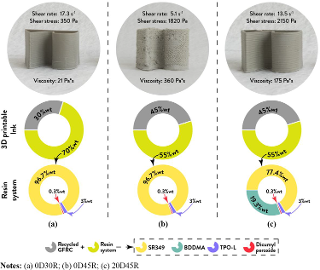
Compositions, three-dimensional printed objects and their corresponding process parameters for three three-dimensional printable inks
3D printed structures were polished and then treated with a gel coat application, smoothing out the texture as well as offering a better aesthetic appearance.
Infill patterns were fabricated with success, and overhangs with a tilt angle of 30° were printed without any need for supports.
“The results of this work show for the first time that a low-cost UV-assisted three-dimensional printing technology can be used for the remanufacturing of GFRCs and some complex structures were printed as a proof-of-concept,” concluded the researchers. “This study opens the way towards the re-introduction of GFRC waste from diverse application fields (e.g. wind turbines blade and construction components) to the production cycle of high-performance composites.”
Recycling in 3D printing is an expansive topic today, from comparing materials to bringing thermoplastics full circle, and even recycling nuclear materials.
What do you think of this news? Let us know your thoughts; join the discussion of this and other 3D printing topics at 3DPrintBoard.com.
[Source / Images: ‘Remanufacturing of end-of-life glass-fiber reinforced composites via UV-assisted 3D printing’]Subscribe to Our Email Newsletter
Stay up-to-date on all the latest news from the 3D printing industry and receive information and offers from third party vendors.
You May Also Like
Gorilla Sports GE’s First 3D Printed Titanium Cast
How do you help a gorilla with a broken arm? Sounds like the start of a bad joke a zookeeper might tell, but it’s an actual dilemma recently faced by...
Nylon 3D Printed Parts Made More Functional with Coatings & Colors
Parts 3D printed from polyamide (PA, Nylon) 12 using powder bed fusion (PBF) are a mainstay in the additive manufacturing (AM) industry. While post-finishing processes have improved the porosity of...
$25M to Back Sintavia’s Largest Expansion of Metal 3D Printing Capacity Since 2019
Sintavia, the digital manufacturing company specializing in mission-critical parts for strategic sectors, announced a $25 million investment to increase its production capacity, the largest expansion to its operations since 2019....
Velo3D Initiates Public Offering in a Bid to Strengthen Financial Foundations and Drive Future Growth
Velo3D (NYSE: VLD) has been among a number of publicly traded 3D printing firms that have attempted to weather the current macroeconomic climate. After posting a challenging financial report for 2023,...