A farmer delivered freshly harvested rubber latex from his plantation to sell at Ban Phraek Ha Agricultural Cooperative in Phatthalung's Khuan Khanun District. When it arrived, the staff of the co-op weighed the milky liquid, checked its concentrate in a small laboratory, and paid the farmer.
"I like the co-op system. As a member of the co-op, I can sell my field rubber latex to them every day. Although they pay me the market price, I am certain that I am not cheated because the digital scale gives the true weight, and the way they measure the latex concentrate is accountable," said Phan Thongkhao. Now in his 70s, the farmer looked at his 170 baht earnings while sipping coffee and eating rambutan at the co-op coffee corner.
Phan, who has been a rubber farmer for more than 40 years, struggles to make ends meet, just like other rubber farmers, although natural rubber is one of the country's bread-and-butter exports. Thailand has been the world's largest natural rubber supplier since 1991, according to the Board of Investment.
Last year, over 4 million tonnes of natural rubber was produced in the country, most of it for export. The rubber generated about 142 billion baht, accounting for 34.8% of the world's total natural latex production, leading competitors like Indonesia, Malaysia and Vietnam. Yet farmers who grow rubber trees for latex have been suffering from low prices. The cabinet is planning to launch the price-guarantee scheme at 60 baht per kilo, compared to the current average market price of 39 baht per kilo.
However, the government programme is not the right solution. One farmer says that if rubber farmers know how to add value by creating their own branded products instead of selling natural rubber latex, they can have more income without waiting for the government's help.
Anun Junrat is the person who wanted to help his community. He founded Ban Phraek Ha Agricultural Cooperative in 2015 in order to open a latex factory. Unlike other latex factories, which produce either latex concentrate or latex pillows, the facility in Ban Phraek Ha is a one-stop service. As of now, it is the only latex factory in Thailand that provides a full production process including making latex concentrate and products in one place.
The co-op has more than 300 members, or half of all rubber farmers in the provinces. The plant produces latex pillows and mattresses under its Talung Latex brand. It is also an original equipment manufacturer (OEM) for another five companies. The product highlights are white colour, less chemical odour and soft texture. Thanks to a research team from the National Science Technology Development Agency (NSTDA), they have improved the product quality and working environment, and shortened production time and cost.
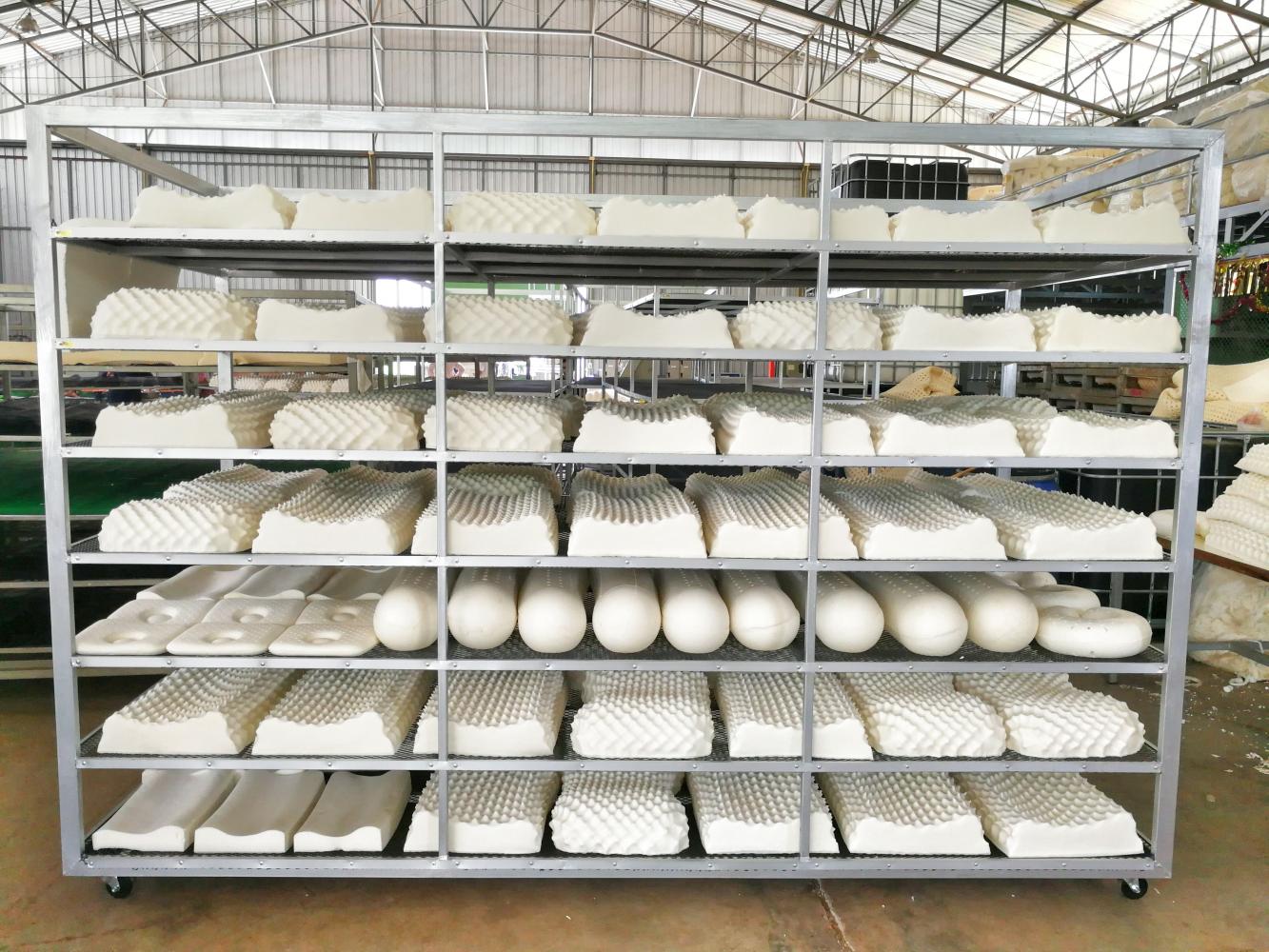
Pillows are left to dry after being removed from the oven. The National Science Technology Development Agency
RECEIVING FINANCIAL WINDFALL
Back in 2013, the head of the Agricultural Extension's Phatthalung Office had a plan to help rubber farmers by having a one-stop factory, starting from buying natural rubber directly from farmers, stocking the latex, and producing latex concentrate. The project got approval in 2014 with a budget of 34 million baht. The authority selected to work with the strongest farmer group was Phanom Wang Agricultural Cooperative in Khuan Khanun district. The problem was that the project did not pass the public hearing, as rubber farmers in Phanom Wang did not want a factory in their backyard.
Anun, who was the deputy manager of the co-op at that time, studied the project. He saw it as a "golden opportunity" to help rubber farmers in his hometown. He sought advice from the community leader of Ban Phraek Ha, located about 10km from Phanom Wang. The leader supported his idea.
"There was no such project in the Kingdom that could fully support the rubber farmers from the start to finish of products like this one," said Anun, adding it was a huge government investment hardly seen in his lifetime, so he took the opportunity.
Anun registered the Ban Phraek Ha Agricultural Cooperative with 50 members in 2015. He asked one member to allow the co-op to own a 10 rai plot of land on the rubber plantation in order to use the land to apply for a loan to build a factory. The machines were set up in late 2016, but no one knew how to operate them.
Starting with a few staff, Anun learned largely by trial and error during the first half of 2017. Although they successfully produced latex pillows, they were not pleased with the quality and did not yet know how to make latex concentrate.
"We are the rubber farmers. We know how to grow rubber trees and get the sap, but not to make latex concentrate for products," he said.
The co-op contacted the National Science Technology Development Agency (NSTDA) for help. A first research team visited the plant in the middle of 2017. At that time, the plant expanded to 30 staff. The research team trained them in how to make latex concentrate until the co-op started purchasing natural rubber directly from its farmer members.
Although it seemed that the co-op could run the full process of a latex pillow business, Anun knew that he could make it better.
"Our latex pillows look like those of other suppliers or imported products -- I want to find a new selling point," he said.
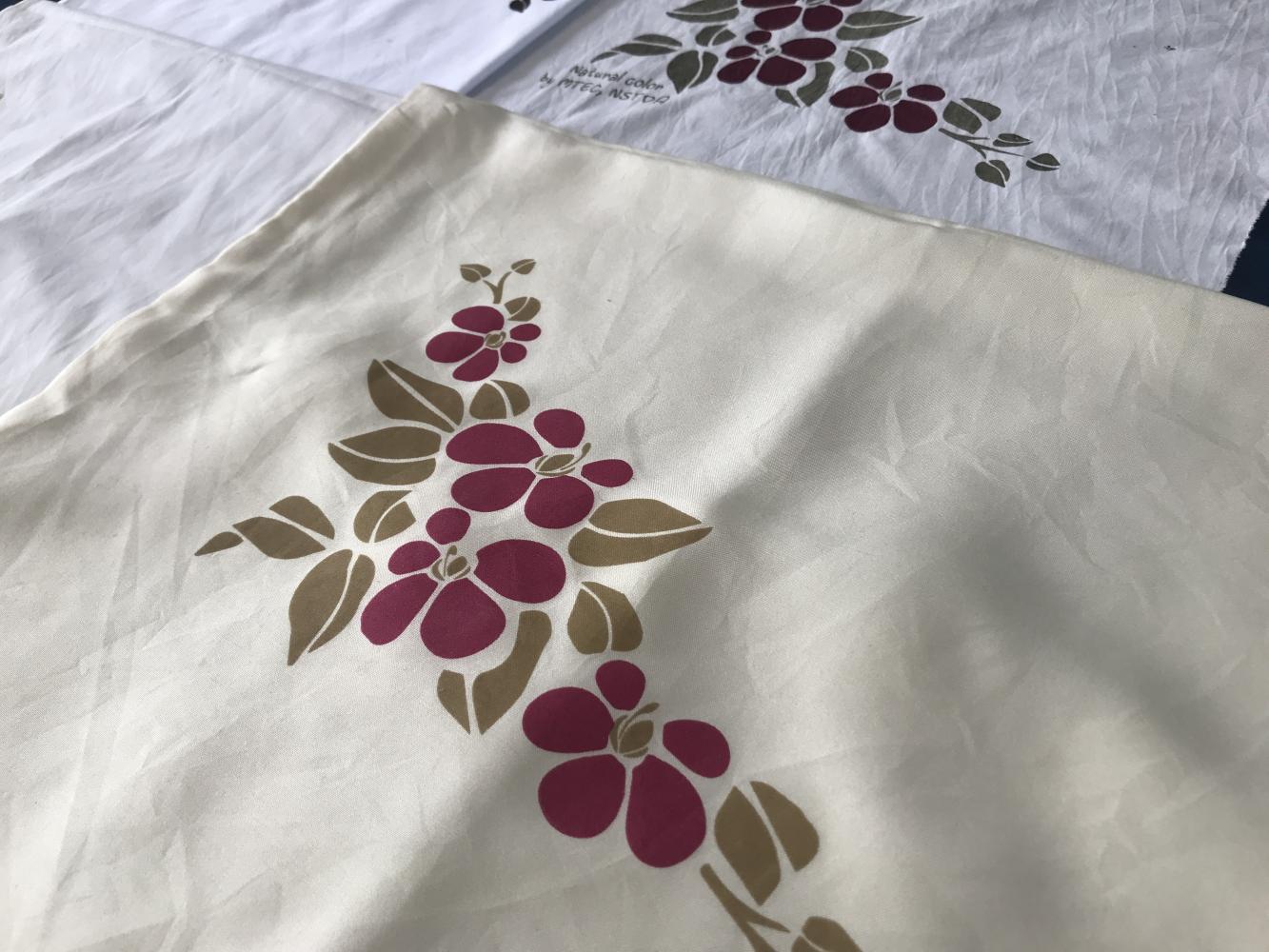
A new pillow case with natural-colour paintings. Karnjana Karnjanatawe
INTRODUCING A NEW FORMULA
Making a latex pillow or mattress usually requires almost a month. It starts from collecting fresh natural latex from farmers, spinning out water from the rubber content, making latex concentrate, ageing it, and then turning it into latex foam for pillows or mattresses.
In the process of latex concentrate and maturation, chemical additives like ammonia, zinc oxide (ZnO) and tetramethylthiuram disulphide (TMTD) are used as preservatives.
To keep rubber latex from being spoiled, it needs 0.3-0.7% of ammonia per total weight. Ammonia is a colourless, highly irritating gas with a suffocating and pungent odour. Exposure to the ammonia even in lower concentrations can cause coughing along with nose, throat, eye and skin irritation.
"Workers in rubber plants have direct contact with ammonia daily. It can make them sick in the long term," said Chaveewan Kongkaew, the principal researcher of the National Metal and Materials Technology Center (Mtec) operated under NSTDA.
She and her team created a new formula to reduce the use of ammonia by half, or down to 0.15%, while still maintaining the ZnO and TMTD at 0.05%.
They call the new latex concentrate ParaFIT. "Para" short for yang para, or "rubber latex" in Thai, and "FIT" stands for Foam Innovation of Thailand.
"ParaFIT is an ultra-low ammonia-latex concentrate. It can help improve the working environment, which will benefit the health of workers," said Chaveewan.
About two years ago, when the business of making latex pillows started to boom, the team looked for a factory that could benefit from the new formula.
"We chose to work with Ban Phraek Ha Agricultural Cooperative because their factory has a complete production line. We also want our R&D to benefit local communities, not a private company," she said.
In a year-and-a-half, the research team visited the factory about 10 times. Each time, they spent about a week. During the first few visits, they adjusted the formula and gradually trained the factory staff until they could manage to produce ParaFIT and perfect their products.
"ParaFIT can shorten the maturation time of latex concentrate from 21-25 days down to 1-3 days. When the time for ageing latex is shorter, it helps reduce costs and storage space," said Anun, adding that ParaFIT can help save at least 3 million baht for each production batch.
"When the maturation time is short, it also benefits the colour of latex foam. Our pillows and mattresses are snowy white, not the eggshell colour of typical latex pillows. The products also do not have the unpleasant smell of chemicals, because when we use little of the additives, they are all washed away during the production process," said Anun.
The factory has also implemented a water-treatment system to recycle water for plants.
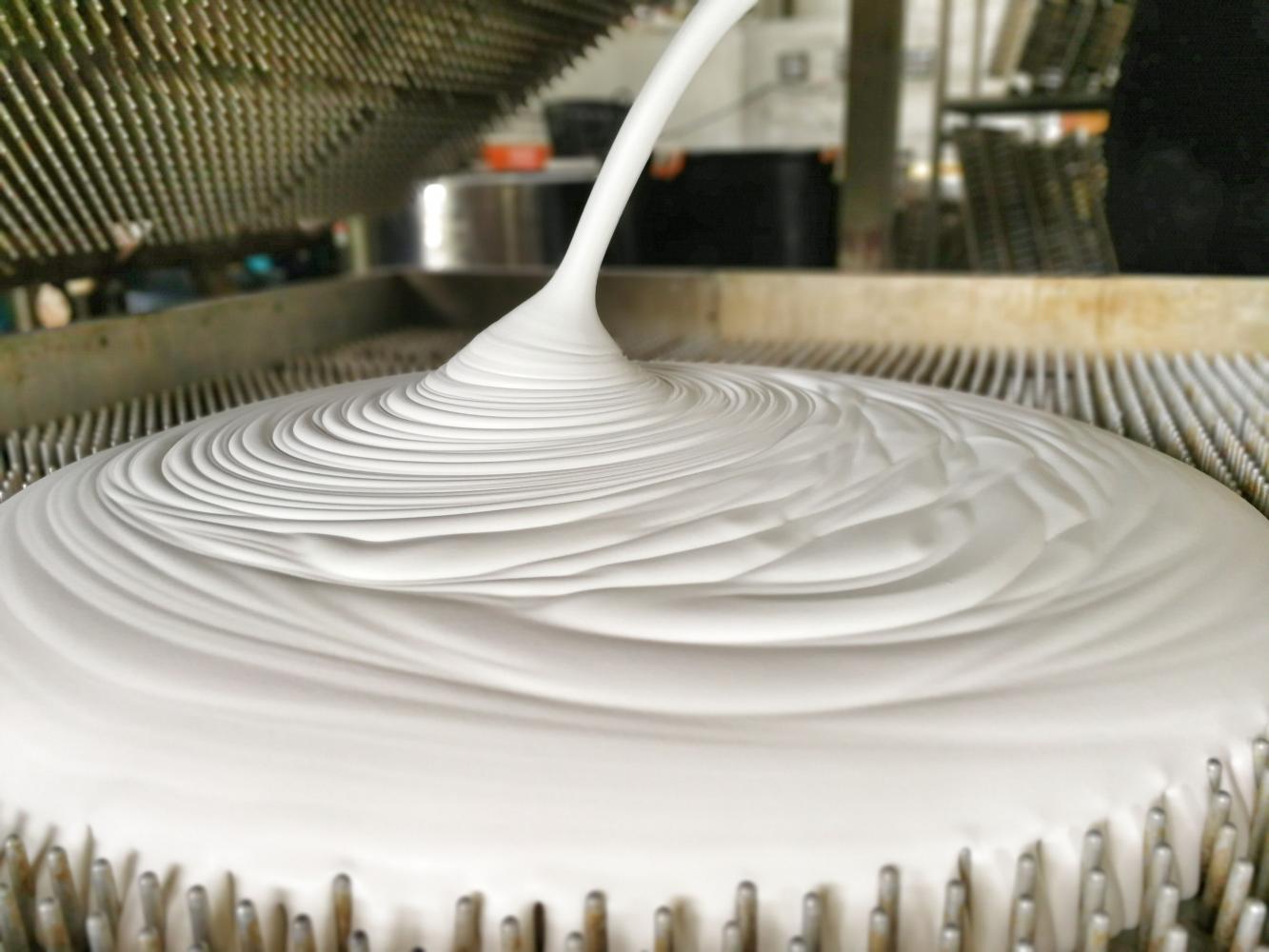
Milky latex liquid is poured into a mattress mould. Photo courtesy of The National Science Technology Development Agency
BEING A LEARNING CENTRE
The demand for latex pillows has increased globally due to a rising awareness of the health benefits. It is estimated that the market, which was valued at about 8.5 billion baht in 2018, will grow 4.9% yearly from 2019-25.
For Thailand, the biggest market for latex-pillow customers is China. Although the Talung Latex brand of Ban Phraek Ha Agricultural Cooperative has not yet exported its own products, some of its OEM partners do. "We will invest more to upgrade our factory to meet both local and international standards, so that we can have direct contracts to produce latex pillows and mattresses for export," said Anun.
During this time, Anun has opened the factory as a learning centre. He has received guests from many parts of Thailand, some neighbouring countries, and also from China.
He can demonstrate every process to those who are interested, especially agricultural co-ops. At present, Ban Phraek Ha Agricultural Cooperative has the capacity to produce 400 latex pillows and six king-size mattresses a day. The products have three levels of firmness. The softest one is like a fine sponge.
"Once, I received guests from China. They put a fresh egg on my mattress and sat on it. The egg didn't crack. It's the way the customers tested the softness, and we passed," he said.
In the future, Anun plans to increase the ParaFIT production capacity from 2 tonnes to 8 tonnes, opening more opportunity for farmers to sell their natural rubber to the co-op. New pillow moulds will be added to create more product choices.
"Our factory has come this far due to the help of the NSTDA. Without the research team, we were like untrained fighters. Working with the researchers, they are like our coaches. They help shape our ideas and make our products better and safer. I don't know what will lie ahead, but I know if I continue on this path, our factory will break even in the next two years," he said.
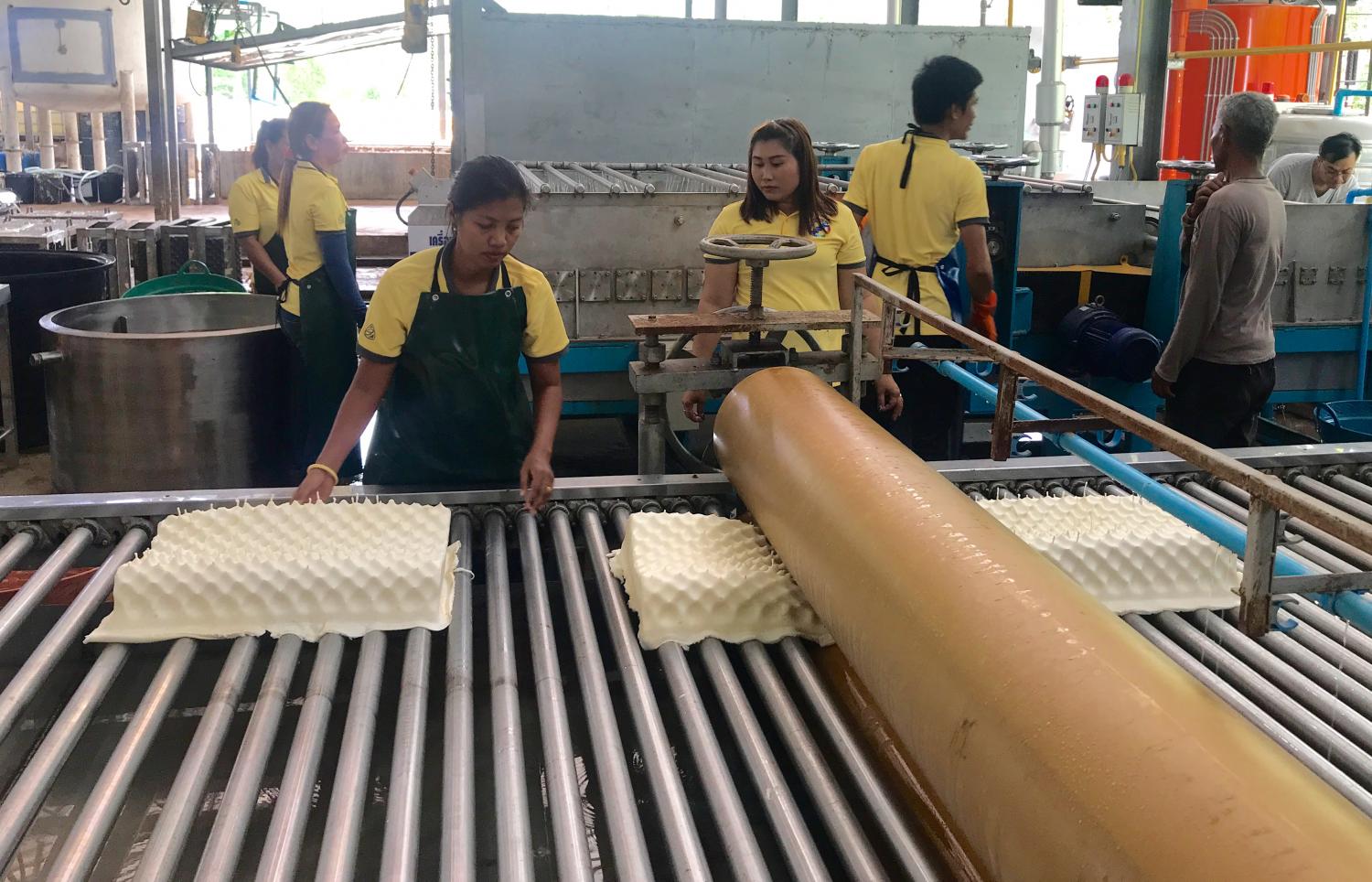
Each pillow is pressed to remove water after being washed. Photos: Karnjana Karnjanatawe
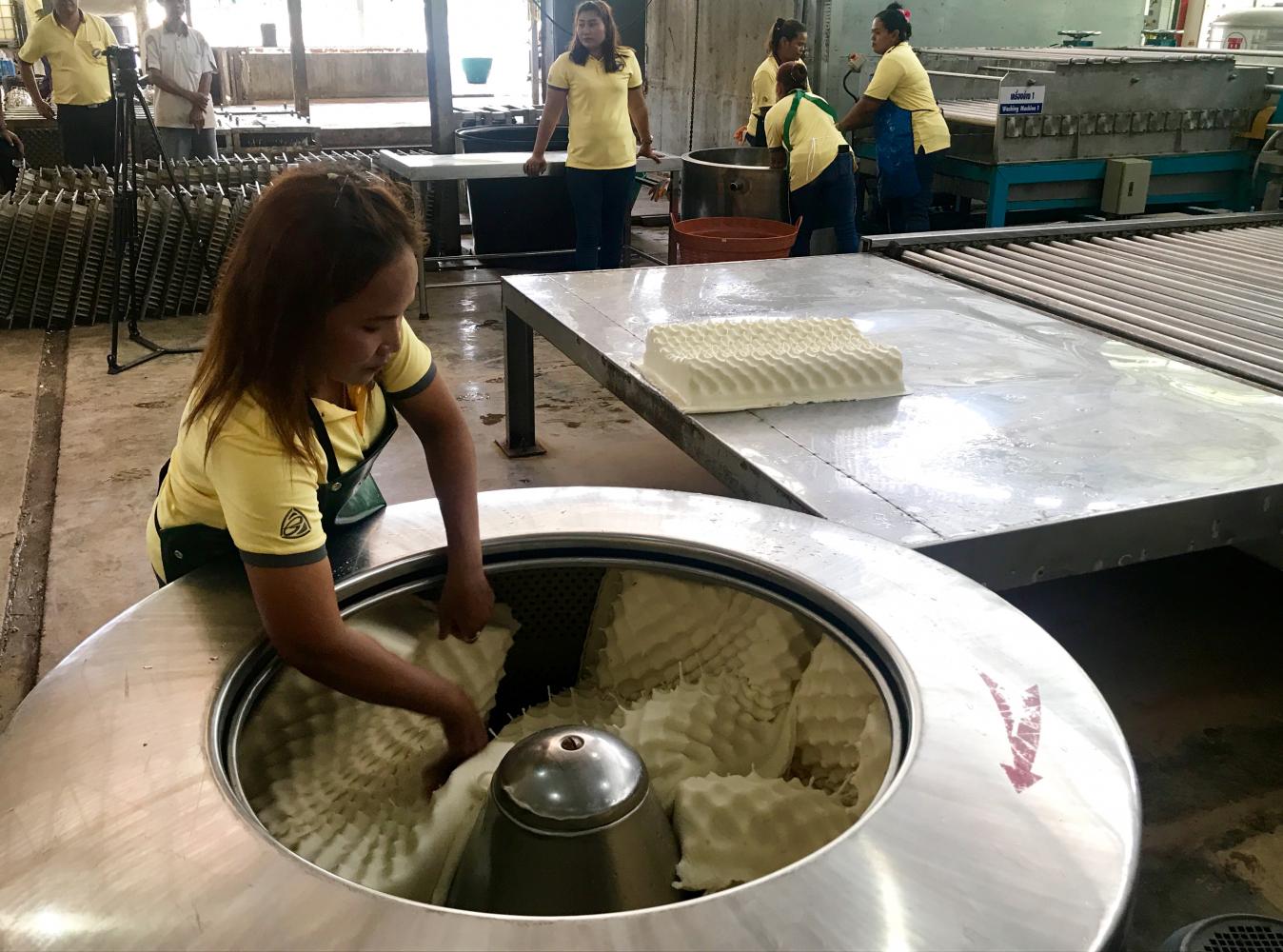
Pillows are spun in the machine until almost dry. Karnjana Karnjanatawe
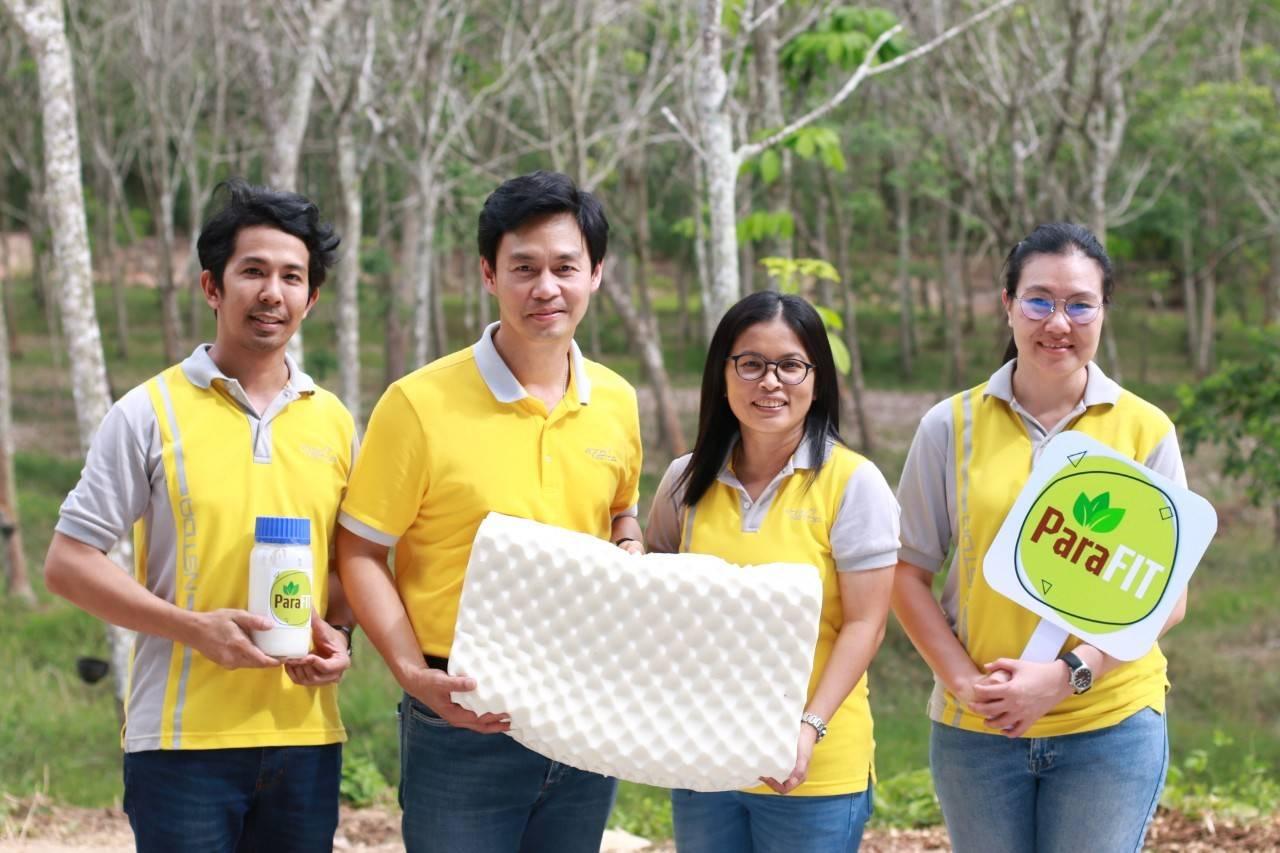
The research team includes, from left, Suriyakamon Montha, Julathep Kajornchaiyakul (Mtec executive director), Chaveewan Kongkaew (research principal) and Piyada Suwandittakul. The National Science Technology Development Agency
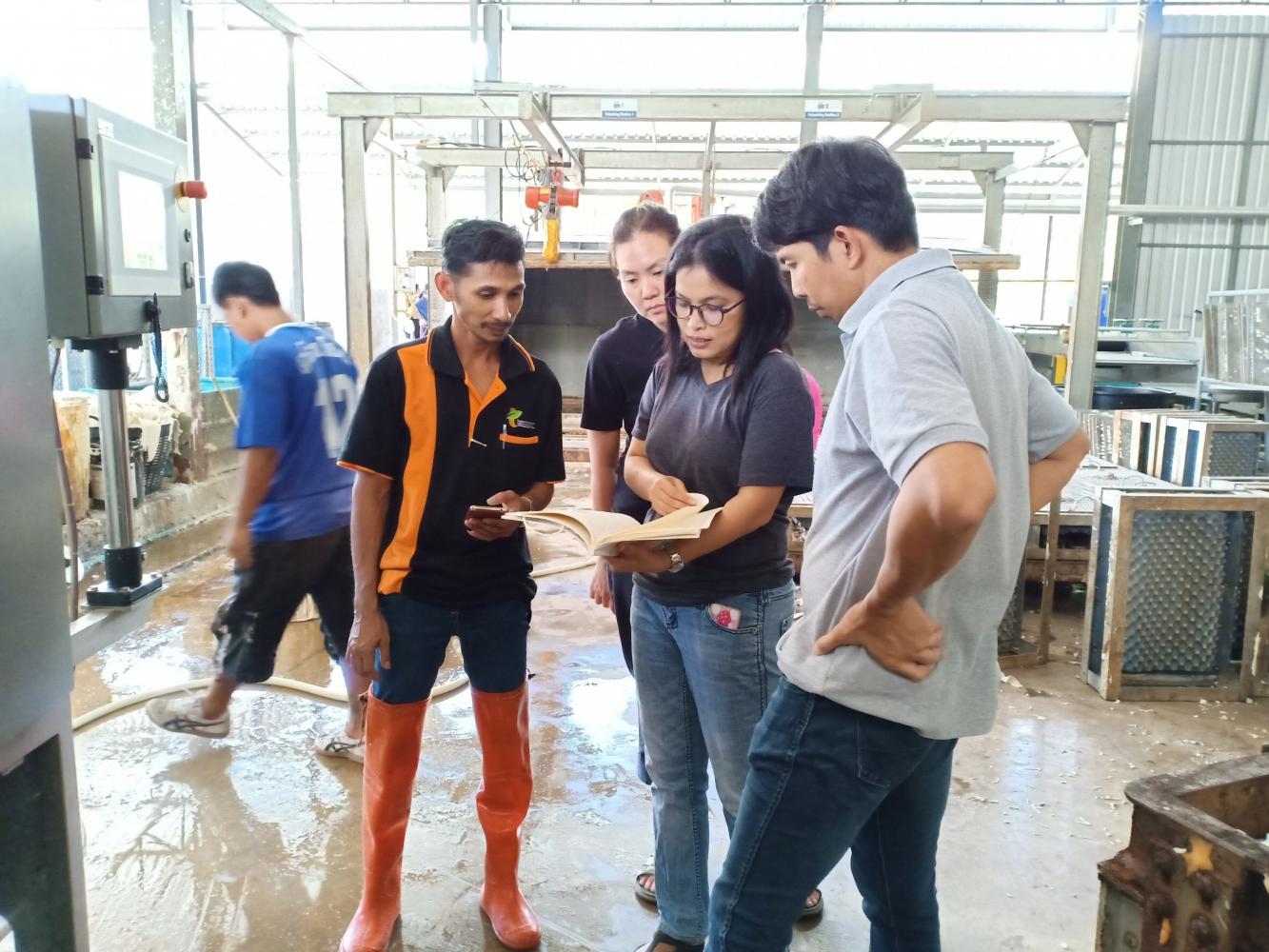
Chaveewan Kongkaew, centre, works with staff at the factory. The National Science Technology Development Agency